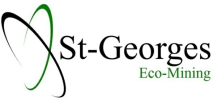
Montréal, July 25, 2022 – St-Georges Eco-Mining Corp. (CSE: SX) (OTCQB: SXOOF) (FSE: 85G1) is pleased to provide a detailed update on the different initiatives undertaken by the Company as well as its strategic realignment.
In parallel with a significant rebranding effort being currently conducted with the branding firm BrandBourg, the Company has reviewed its budget and resources allocation for the coming 24 months. The financial and human resources of St-Georges will endeavor to explore further its Manicouagan project, its metallurgical initiative with energy producers in Iceland, and the deployment of EVSX battery recycling industrial operations.
It is important to note that the hydrogen subsidiary has a self-contained budget and is looking at alternative sources of financing. The Company also started generating revenues in July from the commercial rent linked to a building acquired in Baie-Comeau.
Battery Recycling – EVSX
In June 2022, the Company completed the initial design and engineering of its Phase I industrial circuit for battery preparation and processing into black mass. Company management’s experience in industrial equipment design, maintenance, and operations allowed it to accelerate from feasibility study to industrial ordering and accelerate industrialization in strategic locations. The modular approach will cost substantially less than what is discussed in the market by many entering the sector. It also allows for a strategy of rapid local and international growth. A portion of the Company’s strategy is to focus on novelty in process and avoid developing new equipment. Off-the-shelf industrial units are being purchased to be incorporated within the rollout, which eliminates risk and learning curves.
Recently, the Company commissioned and disbursed the initial payment for manufacturing three identical battery processing industrial units. These units will be located in three separate locations; one is to be located in Baie-Comeau, QC, and the remaining two are expected to be located in two distinct locations near or within battery aggregation facilities in Québec and Ontario. These two locations are in discussions to partner with EVSX. Each unit will have the potential to process up to 8,500 metric tons of used batteries per year.
The total manufacturing costs are expected to be US$1 million for the three units. Transportation, installation, training, and configuration costs should add $1.5 million to the total resources to be expensed. Building and facilities adaptation costs should add $5 million to the total. The Company expects all three industrial plants will be fully operational within approximately six months. The first industrial plant is expected to come online in the last quarter of 2022.
The equipment will be preassembled and tested prior to shipping to optimize installation costs as well as commissioning efforts. The modular approach reduces risk and superfluous effort in the field while allowing the Company greater flexibility in its approach to its centers of excellence. The Company expects to be in a position to test the circuits at the manufacturer’s facilities near the end of Q3. A contracted engineering firm has been retained for quality control and quality assurance purposes.
These engineers will be present for the bill of lading stage and shipment of the modular units. Operating cost simulations have identified that logistics and transportation will be the most expensive line item of the operations. Additional sites in Iceland, California, and Italy are being researched on a number of criteria, including their proximity to transportation hubs in order to limit logistical costs and complications between EVSX operations and clients for material recuperated in the black mass extraction process.
The process preparation phase requires neutralizing the batteries’ residual electric charges. Palettes of batteries are immersed in a saline solution for 24 to 48 hours to eliminate any residual electric charge.
After dispersing any residual charges, the batteries are shredded. Most of the copper, steel, plastic, carbon, and aluminium is segregated and recuperated. These steps leave the different chemistry types of black mass as the end product. Depending on the type of battery, black mass can comprise between 5% to 20% of the total mass and weight. Steel and copper do not require any further transformation to be sold. Aluminium represents a significant part of the batteries, and third parties have indicated that they would be ready to acquire all of the Company’s production alongside the carbon reduction credits produced by the process. These third parties are also interested in the carbon recuperated at this stage. This carbon is of different grades and quality, depending on the type of batteries being processed. It can be sold to clients in the steel-making industry or converted into briquettes and anodes to be used by aluminium smelters. This new development allows the Company to avoid sending carbon to landfills. Initial projections show that the stage of the operations should be financially self-sufficient, with the possibility of generating a profit.
The different types of black mass will be transported to the associated processing facilities that the Company is planning to build to extract the valuable minerals. The facility targeting the cobalt and nickelrich black mass will be built in Baie-Comeau and located within the limits of the property acquired in full in July by the Company.
Phase II of battery recycling is underway with black mass from battery preparation units for nickel-type and lithium batteries to replicate impurities that may occur in real-life situations, such as mixing different battery chemistry or types. The Company expects lithium batteries to follow a parallel process to its spodumene technology. In contrast, it expects a more compact and economical process for nickel-type batteries via its ‘cold smoke’ technology. Information on this strategy will not be disclosed at this time
The Company has processed a specific quantity of batteries to generate black mass for testing in a thirdparty pilot environment. The results of these independent tests will provide data required for the plant’s industrial layout, the foundry’s environmental assessment, and the information needed to populate related patents.
Company strategy includes using multiple centers of excellence to protect IP and combine the technology islands in one centralized location.
EVSX is expected to finalize its spare parts, operating and maintenance analysis for its operations and have all equipment manual ready to train personnel in Q4. Training, spare parts and optimized preventative maintenance will be organized, recognizing that there is a learning curve with all new personnel and operations.
Intellectual Property – Patents
Three new and distinct IP initiatives will be formally applied for in Q3, covering lithium, lithium batteries, and nickel-type batteries. The Company expects to be in a position to disclose further information on these initiatives as early as mid-Q3. These provisional patent fillings will reinforce the current protection of the company lithium processing technology that is now at the patent pending stage with protection in numerous countries including but not limited to USA, Canada, United Kingdom, Europe, Australia, South Korea, Japan, and Brazil.
Lithium Hydroxide Production
The Company initiated a small production of lithium hydroxide in July. The significant improvements developed alongside this initiative require patent protection. Third-party labs are still testing the technology; early results from producing pure lithium crystals hint at a major breakthrough concerning the cost-effectiveness of the method and indicate a barely noticeable carbon footprint.
“We firmly believe that the process developed is one of the most compact, if not the most compact process, currently being used in the industry, with least environmental footprint with no chemical residues as all the by-products are salable,” commented Enrico Di Cesare, Vice-President Research & Development of St-Georges Eco-Mining.
The conversion of the lithium in solution into lithium hydroxide crystals (LiHO) is agnostic from the source of the lithium concentrate. The Company is now ready to receive material from groups that want to test the potential of their lithium resources in a pilot-plant environment.
Recent results and developments will be integrated into the internal study being conducted to build a proprietary lithium hydroxide production. Spodumene concentrate feedstock for this project is expected to be sourced from the market, domestically and abroad.
The Company now considers the development of the process to produce lithium
from spodumene to be completed & ready for commercialization.
See the lithium hydroxide crystals on Twitter:
https://twitter.com/StGeorgesPlat/status/1546895794086858758?s=20&t=BcwGqVzMbDol2ONl6cKoQ
Commercialization
The Company is now open to third-party requests to run pilot plant trials without regard to material source. A large pilot plant is prepared for extended pilot plant runs.
Alumina production
The Company’s processing technology core value is its ability to convert by-products and reduce the quantity of material being rejected into mineral tailings. The metallurgists continue to work on producing fertilizers from the remaining material contained in lithium concentrates.
The production of high purity alumina has been finalized, and the Company is ready to work with end users. As aluminum smelter grade is easy to achieve but sells for less, the Company is prepared to adjust purity levels for niche applications. The high purity alumina will be equivalent to the lithium hydroxide or carbonate production in total weight.
Discussions are being held with major actors in the steel industry to study the different options to leverage identified synergies. The Company will continue to target non-competing industries and suggest monetizing the waste streams compatible with its process.
“St-Georges is open for business and believes the solution to the problems of spodumene processing in Québec can be addressed and turned into a viable industry. We are proud of achieving this important milestone, and the new patents covering this development will be filed in early August(…)” commented Enrico Di Cesare, Vice-President Research & Development of St-Georges Eco-Mining.
Commercial Electrolysis Equipment
Green Hydrogen Technologies – H2SX
Mineral Exploration Update
Notre-Dame Project, Québec
Julie Project, Québec
Manicouagan Project, Québec
Thor Project, Iceland
“(…) Management has decided on a strategic realignment of prioritizing projects (…) The recent Manicouagan results demonstrate this is where we should be putting our exploration resources at the moment, and our advanced purchase of fuel which has been delivered on-site further defines this priority (…) the realignment will allow us to augment work to better define our targets on Julie, Notre-Dame, and Thor before moving forward with drill programs. This will allow us to vector in on potential targets with greater accuracy while conserving resources (…) This realignment is a strategic shift which helps us preserve our cash position until market conditions improve. At the same time, it allows us to balance the demands on our staff and collaborators as the workload increases for launching the battery recycling side of our business.” Commented Herb Duerr, St-Georges’ President & CEO.
Rebranding and Communication
Branding
Governmental & Public Relations
The Company has also retained the services of two national public relations firms, Ryan Public Affairs and Hill+Knowlton Strategies. Ryan Public Affairs initiated its mandate in July and is tasked with governmental communications and public relations. Hill+Knowlton Strategies has a similar mandate with the addition of the First Nations outreach program.
“(…) Environmentally friendly mining is not an oxy-moron (…) green doesn’t have to be a choice between the environment or your wallet (…) With the new messaging from the communications initiative, we will specifically be targeting ESG funds. (…) We are in discussions with a financial advisors firm with the clear goal to raise St-Georges’ profile with institutional investors (…) the objective being to get these entities to buy in the open market (…) we are also in the process of hiring an ex-fund manager, whose details will be disclosed at a later date. (…)” said Frank Dumas, Chief Operating Officer of St-Georges Eco-Mining.
ON BEHALF OF THE BOARD OF DIRECTORS
“Frank Dumas”
FRANK DUMAS
Chief Operating Officer & Director
About BrandBourg
About Ryan Public Affairs
About St-Georges Eco-Mining Corp.
St-Georges develops new technologies to solve some of the most common environmental problems in the mining sector, including maximizing metal recovery and full circle EV battery recycling. The Company explores for nickel & PGEs on the Julie Nickel Project and the Manicougan Palladium Project on Quebec’s North Shore and has multiple exploration projects in Iceland, including the Thor Gold Project. Headquartered in Montreal, St-Georges’ stock is listed on the CSE under the symbol SX and trades on the Frankfurt Stock Exchange under the symbol 85G1 and on the OTCQB Venture Market for early stage and developing U.S. and international companies. Companies are current in their reporting and undergo an annual verification and management certification process. Investors can find Real-Time quotes and market information for the company on www.otcmarkets.com
The Canadian Securities Exchange (CSE) has not reviewed and does not accept responsibility for the adequacy or the accuracy of the contents of this release.